Easy to Use Laminate Optimization Software
The fastest way to design manufacturable and lightweight laminates that satisfy all analyses for all load cases in minutes. Simply import your FEM and the software guides you through a process to generate global plies according to manufacturabilty rules and failure analysis checks. Your FEM is automatically updated with the sequenced plies and you can export this data to spreadsheets or into CAD such as CATIA.
Express provides the composite engineer an easy to use software interface along with robust optimization for strength, stability, and stiffness helping you to achieve the lightest weight and better performance. Applications include:
- Sporting Goods – Bike frames, snowboards, tennis racquets
- Automotive – Doors, trunks, hoods, body panels, floor panels, body in white
- Medical – Orthopedic prostheses
- Industrial – Robotic end effectors
- Marine – Yachts, sailboats
- Wind Energy – Turbine blades
- Aerospace – Seats, doors, winglets, flaps
The lightest frame for your best ride!
Design Optimization
Use Case
The most frequent use case for Express is to optimize the design of a composite or metal part by determining the optimum thicknesses, ply shapes, ply angles, stacking order, and sandwich cores. Applicable for hand layups like a bike frame, or robotic AFP/ATL like a space launch tank.
Streamline Work Flow
The interface quickly steps you through the process work flow. No training nor user manual is required. The process starts by importing a FEM and the FEA computed stress resultants (element forces). You select the material, analyses to perform, and design criteria such as layup rules, and Express will do the rest as it automatically iterates with FEA (MSC Nastran, NX Nastran, Abaqus, Optistruct) to converge load paths and to resolve buckling and displacement stiffness constraints.
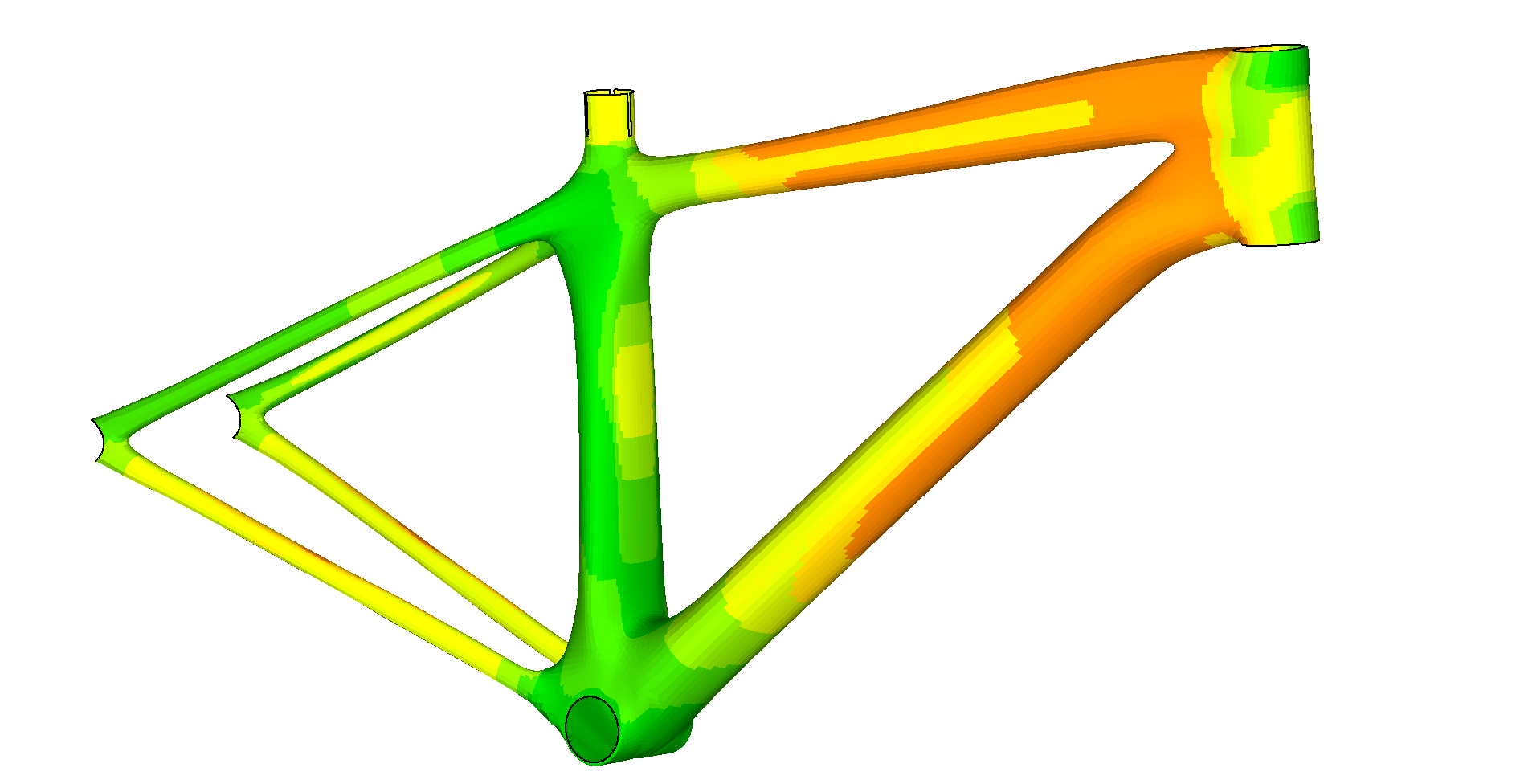
Ply Boundary Optimization
Determining ply boundaries is challenging in composite design. Tailoring ply boundaries by optimizing organic ply shapes to the load path saves weight but increases manufacturing costs. Express optimizes ply boundary patterns interactively. The user can trade weight vs. manufacturability in real-time by visualizing the proposed ply shapes on the mesh.
Visualization
At every step in the process see your design using 3D graphics
- Draw a cut-plane on the FEM and visualize a 2D section cut
- View 3D global ply coverage, the shape and size of each ply layer
- Plot ply drops, adds, and counts
Laminate Sequencing
Once ply boundaries are established, the stacking sequence of the global laminate plies is optimized. At every step in the process, real-world design constraints are included such as:
- Ply percentage limits
- Balance and symmetry
- Max adjacent plies
- Full assembly plies
- Reduced ply drops/adds
Optimization Criteria
Express satisfies all strength and closed form buckling failure criteria during the optimization. These analyses are described below. Additionally, Express can extract FEA eigenvalue solutions and identify which elements are in the buckling mode to stiffen just them. The user can also identify a displacement limit for any grid in the FEM.
Analysis Check
Use Case
Another Express use case is to perform an analysis check of a part with your selected failure criteria from the many possible choices the software provides.
Streamline Work Flow
The interface quickly steps you through the process work flow which is even more streamlined than the design optimization use case. During FEM import, the analysis use case imports the laminates (for example, Nastran PCOMG or Abaqus General Section) and a material identifier that relates directly to a material in the HyperSizer database. Once the FEM design is imported, along with the corresponding FEA forces, Express displays controlling failure analyses, load cases, and critical safety margins.
Failure Analyses
For composite materials, Express offers strength failure criteria on the ply basis such as max strain, max stress, and Quadratic theories such as Tsai-Hill, Tsai-Wu, and physics based solutions such as Hashin and Puck. These can have ply based correction factors for their allowables. Laminate based failure criteria such as open hole compression (OHC), filled hole tension (FHT) are also provided. All allowable data can be defined as function of %45 plies, or using the AML, or polynomial approach. Sandwich failure analyses are also provided such as max shear stress, facesheet wrinkling and dimpling. Metal analyses include Von mises yield, max principal stress, etc.
Compatible with Pro
Express can be used throughout product development and final analysis. HyperSizer Pro users can seamlessly open an Express database without any loss of data or time to further mature their design. All of the data entered and computed with HyperSizer Express automatically transitions to HyperSizer Pro.
Express in Action
Composite Bike Frame
Strength and Stiffness Laminate Optimization including manufacturable ply shapes
Can’t see the video? View here
The ultimate software tool for analysis & design of composite laminates, honeycomb, and foam sandwich panels